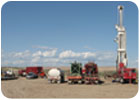
A trip to Salt Lake City-based Major Drilling America Inc. included an excursion to Vernal, Utah, a scenic, nearly 200-mile drive east through the mountains to the oil fields. Meeting me there was Curt Marrington, a drilling supervisor for Major, who is in his 15th year with the firm, having been through two ownership changes – Tonto Drilling-to-Dynatec Mining, and Dynatec-to-Major.
“I started out as a very green driller’s helper, and worked my way up to driller,” Marrington relates. “A lot of our work at that time was mineral exploration, and when the price of gold went way down, things would get slow, so I’d do some underground mining, as well as working for the raised-bore division. Then, when things picked up again, I went back to drilling.”
The customer of the Vernal job site: EOG Resources, one of the largest independent (non-integrated) oil and natural gas companies in the United States. “We’re drilling 2,500-foot rat holes – pre-collar holes for the big oil drills,” Marrington explains. “We drill 121⁄4-inch holes down to 2,500 feet, set 95⁄8-inch casing and cement it in. Then the big rigs come in and drill down to 16,000 or however deep to get to the gas and oil.
“We’re using a fairly new Schramm T-130 – those are nice machines. We’ve got eight of them; we’d have nine, but one was sent down to our Chilean operation. And we’re running what they call a 12-inch hammer – I think it measures out to 103⁄4 inches – and a 12-inch hammer bit.”
I’d like to think that maybe I was some sort of good luck charm, but more likely I just happened to show up at the right time. “We’re pretty happy,” says Marrington. “We’ve been fairly fortunate in that we just drilled two 2,500-foot holes, and we took them all the way down with the hammer, which is excellent. A lot of times, we’ll hit water, and we’ll have to switch over to a rock bit, a tri-cone. That happens probably 80 percent of the time. And that means about a four-hour roundtrip, depending, of course, on the depth where you water out at. We run 8-inch collars, which are 150 pounds per foot, and it takes a little while to get those torqued up. We don’t run the 8-inch collars with the hammer because we don’t need the weight. But when we run that cone, we definitely need the weight and the stabilization right on top of the bit. So those dry holes mean fewer headaches.” He says, on average, they’ve been getting about 7,000 feet on a hammer bit.
“With all the air that we have, we’re pushing about 2,500 cfm, and we can take it up to about 1,200 psi with our booster. Rarely in a dry hole like that do we push more than 400 pounds with the hammer, but we do have the booster there in case we hit the big water and need the pressure to lift that column of water.”
The hole I saw being drilled took three and a half days to complete, about average according to Marrington. “We’ve been poking holes pretty steadily on this site, and we’re happy if we can get two holes a week. We usually run two four-man crews, 7 o’clock to 7 o’clock.”
Work at this site began in February 2007. “It’s hard to say how long we’ll be out here,” Marrington muses. “There’s nothing set in stone; we don’t have X amount of holes or X amount of footage to drill. As long as they have holes for us, we’ll keep drilling them. EOG has a lot of drill rigs going, and we need to keep ahead of them. There are two other drilling contractors out there doing the same thing we do. They’re both based in Vernal, so we’re the new guys in town – not always easy.”
And Marrington is happy to be on this project for the foreseeable future. “I really like drilling with the hammer,” he says. “For a lot of our drilling in Wyoming, for example, the ground isn’t hard enough, so we’d have to run PDCs or tri-cones. That’s one of my favorite things – hearing that hammer beat; I love the raw power.” And commenting on his overall situation with his firm, he beams, “Major is a great company; we’re treated very well. They’ve provided us with great equipment, and we couldn’t be happier.”
Sounds like a very good setup for everyone involved.
ND
“I started out as a very green driller’s helper, and worked my way up to driller,” Marrington relates. “A lot of our work at that time was mineral exploration, and when the price of gold went way down, things would get slow, so I’d do some underground mining, as well as working for the raised-bore division. Then, when things picked up again, I went back to drilling.”
The customer of the Vernal job site: EOG Resources, one of the largest independent (non-integrated) oil and natural gas companies in the United States. “We’re drilling 2,500-foot rat holes – pre-collar holes for the big oil drills,” Marrington explains. “We drill 121⁄4-inch holes down to 2,500 feet, set 95⁄8-inch casing and cement it in. Then the big rigs come in and drill down to 16,000 or however deep to get to the gas and oil.
“We’re using a fairly new Schramm T-130 – those are nice machines. We’ve got eight of them; we’d have nine, but one was sent down to our Chilean operation. And we’re running what they call a 12-inch hammer – I think it measures out to 103⁄4 inches – and a 12-inch hammer bit.”
I’d like to think that maybe I was some sort of good luck charm, but more likely I just happened to show up at the right time. “We’re pretty happy,” says Marrington. “We’ve been fairly fortunate in that we just drilled two 2,500-foot holes, and we took them all the way down with the hammer, which is excellent. A lot of times, we’ll hit water, and we’ll have to switch over to a rock bit, a tri-cone. That happens probably 80 percent of the time. And that means about a four-hour roundtrip, depending, of course, on the depth where you water out at. We run 8-inch collars, which are 150 pounds per foot, and it takes a little while to get those torqued up. We don’t run the 8-inch collars with the hammer because we don’t need the weight. But when we run that cone, we definitely need the weight and the stabilization right on top of the bit. So those dry holes mean fewer headaches.” He says, on average, they’ve been getting about 7,000 feet on a hammer bit.
“With all the air that we have, we’re pushing about 2,500 cfm, and we can take it up to about 1,200 psi with our booster. Rarely in a dry hole like that do we push more than 400 pounds with the hammer, but we do have the booster there in case we hit the big water and need the pressure to lift that column of water.”
The hole I saw being drilled took three and a half days to complete, about average according to Marrington. “We’ve been poking holes pretty steadily on this site, and we’re happy if we can get two holes a week. We usually run two four-man crews, 7 o’clock to 7 o’clock.”
Work at this site began in February 2007. “It’s hard to say how long we’ll be out here,” Marrington muses. “There’s nothing set in stone; we don’t have X amount of holes or X amount of footage to drill. As long as they have holes for us, we’ll keep drilling them. EOG has a lot of drill rigs going, and we need to keep ahead of them. There are two other drilling contractors out there doing the same thing we do. They’re both based in Vernal, so we’re the new guys in town – not always easy.”
And Marrington is happy to be on this project for the foreseeable future. “I really like drilling with the hammer,” he says. “For a lot of our drilling in Wyoming, for example, the ground isn’t hard enough, so we’d have to run PDCs or tri-cones. That’s one of my favorite things – hearing that hammer beat; I love the raw power.” And commenting on his overall situation with his firm, he beams, “Major is a great company; we’re treated very well. They’ve provided us with great equipment, and we couldn’t be happier.”
Sounds like a very good setup for everyone involved.
ND
Report Abusive Comment