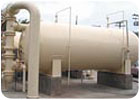
Arsenic's evil reputation is manifested in its old alchemists' symbol - a coiled serpent ready to strike. Considering arsenic's eminence as the preferred homicidal agent of detective novels, it is not surprising there is a great deal of anxiety over its possible presence in water, among other substances, we use on a daily basis. This article addresses the various unit operations available for its removal from water.
The Environmental Protection Agency (EPA) has identified a number of treatment options for the removal of arsenic as the best available technology. Listed and discussed below, in no particular order of applicability, preference, efficiency or treatment cost, are some of the processes under consideration.
Reverse Osmosis
This membrane process primarily is designed for the desalting of saline or brackish waters by the application of hydrostatic pressure. This overcomes osmotic pressure and drives the water to be treated through a semi-permeable membrane designed to allow passage of water, but not of dissolved contaminants. The process requires expensive and fragile membrane stacks, either cellulose acetate or thin film composite. Cellulose-acetate membranes can be operated at up to 400 psi, but are subject to biological attack and hydrolysis. They also allow the salt passage to double after a service life of about three years. The more expensive thin film composite membranes are capable of the same or greater flux rate, but at half the applied pressure. These allow only a less than 30 percent increase in salt passage after three years. Both require considerable pre-treatment to prevent scaling, plugging and colloidal or biological fouling of the membranes.
Since the recovery of product water, as a percentage of feed water, is a function of applied hydrostatic pressure (up to 400 psi or more), the process tends to be quite energy-intensive. Most reverse osmosis plants are designed for 75 percent to 80 percent recovery, i.e., up to 25 percent of the flow must be disposed of as a concentrated, possibly hazardous, waste. Reverse osmosis is quite capable of the removal of arsenic to very low levels. Process operation and maintenance costs, as well as labor intensity, will tend to rule out its application for all but small volume treatment systems.
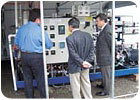
Granular Ferric Hydroxide
Granular ferric hydroxide (GFH) is an absorptive medium designed for the removal of arsenic, phosphates, chromium and other heavy metals. Raw water pH and contaminant concentration (e.g., iron, manganese, chromium, organics, silica, phosphates, etc.) determine the life of the media. Preoxidation of raw water is not required, and both arsenic valence states are removed. Periodic backwashing of the media is required depending on raw water quality. GFH is presently classified as a non-regenerative media that must be removed from the filter vessel when exhausted, and replaced with new media. Research is being conducted to determine the feasibility of regenerating GFH. Spent GFH media is disposed of in a landfill. State regulations should be consulted to verify acceptable testing methods and media disposal requirements.Ion Exchange
Capable of complete removal of all dissolved matter including arsenic from water, this process is widely used for the production of de-ionized water. One great advantage of ion exchange is that no pH adjustment is necessary. Recent advances in resin technology have replaced the weak-base anion resins with strong-base ones. Pentavalent arsenic (As+5), being present as the divalent anion HAsO4-2, appears to have a greater affinity for this type of resin. Strong base resins permit the use of ordinary sodium chloride brine for regeneration, and eliminate the need for the use of strong acids. Regeneration is a slow and water-intensive process. Typically, columns are rinsed with one-bed to two-bed volumes to displace the regenerant. This is followed by a fast rinse for about 10 minutes at design flow. The used regeneration brine, containing arsenic, is a hazardous waste and must be disposed of accordingly.Activated Alumina
Activated alumina has a long history of use as an adsorptive treatment technology for arsenic removal. The media is a byproduct of aluminum production. It primarily is an aluminum oxide that has been activated by exposure to high temperature and caustic soda. The material is extremely porous and has a high average surface area per unit weight. The capacity for arsenic removal by activated alumina is pH-dependent, with the maximum removal capacity achieved at pH 5.5. Adjusting the pH of the source water, therefore, provides removal capacity advantages. As the pH deviates from the 5.0 to 6.0 range, the adsorption capacity for arsenic decreases at an increasing rate. Process demonstrations have shown that arsenic removal capacity has been reduced by more than 15 percent at pH 6.0, compared to that of pH 5.5.Fluoride, selenium and other inorganic ions and organic molecules also are removed by the same pH-adjustment activated alumina process. The process, however, is preferential for arsenic at the optimum pH level of 5.5. Other ions that compete with arsenic for the same adsorptive sites at other pH levels are not adsorbed in the pH range of 5.0 to 6.0. Included are silica and hardness ions that are adsorbed in the pH range of 7.0 to 10.0.
Activated alumina either can be regenerated or can be replaced with new media when the selected breakthrough point is reached. At the optimum pH for arsenic removal, fluoride, selenium, some organic molecules, and some trace heavy metal ions are adsorbed; however, these also are completely regenerated along with arsenic. Because these ions compete for the same adsorptive sites with arsenic, their presence might deplete the alumina capacity for arsenic. When excess fluoride and arsenic are present in the water supply, a special treatment technique is required.
The adsorptive capacity of many adsorptive media, particularly activated alumina, is pH-sensitive; removal capacity increases with decreasing pH. Employing pH adjustment, therefore, generally provides cost advantages regardless of whether the media is regenerated or replaced. Because the pH adjustment chemicals usually are the same chemicals that are used for regeneration, it generally is advantageous to couple regeneration with pH-adjustment systems when the media can be regenerated.
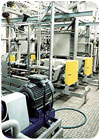
Lime Softening
Excess lime softening is the addition of a sufficiently high lime dosage, at times in excess of 1 gram per liter, to obtain a pH greater than 11.5. It has long been used for the removal of calcium and magnesium carbonate hardness, and also is capable of the removal of approximately 90 percent of any arsenic that may be present.
The removal of trivalent arsenic appears to be dependent upon the precipitation of magnesium hydroxide. The addition of powdered activated carbon, though, apparently not absolutely necessary, appears to enhance removal efficiency. While this is an old tried and true process, and while apparently quite capable of arsenic removal, the process remains plant and chemical intensive, requires the recarbonation of the water, and produces large volumes of sludge. For these reasons, unless there also is a demonstrated need for softening, the process may not be deemed economically viable.
Coagulation-filtration
Conventional coagulation/flocculation/filtration, using iron salts, is effective in the removal of up to 90 percent of arsenate at pH levels of 7 or less. Above a pH of 7, flocs from iron salts effectively remove arsenic. Iron coagulants will remove about 50 percent of trivalent arsenic. Thus, it is very important to fully oxidize trivalent arsenic to arsenate with chlorine or another strong oxidant prior to coagulation.High arsenic concentrations frequently are found in anaerobic waters. These same waters generally are high in ferrous iron and manganous manganese, necessitating their removal. Iron and manganese removal processes relying on the oxidation, and subsequent precipitation of the metals as hydroxides, also will effectively remove soluble arsenic by co-precipitation and/or adsorption reactions. It is almost as though the presence of the iron and manganese to be removed is analogous to a natural coagulant addition, as it facilitates the removal of arsenic. Removals of soluble arsenate during ferrous iron oxidation and precipitation processes are very significant. This likely is not the case during soluble manganese oxidation alone. In such cases, the addition of iron salts is indicated.
Of the arsenic removal processes available and discussed herein, iron coagulation, whether practiced primarily for the removal of arsenic, or also of iron and manganese, appears to be the most promising and proven process available. This process is capable of the removal of 90 percent or more of any arsenic present. Furthermore, many such plants already are in existence, and operating efficiently, even though initially they were designed for the removal of iron and manganese only.
Some iron and manganese removal processes rely on a proprietary adsorptive media for their removal efficiencies. In these systems, the iron/manganese (along with any arsenic present) are oxidized, and then the iron and manganese are precipitated as hydroxides, adsorbing arsenic. A second adsorptive reaction occurs at the water/media interface where localized zones of high pH assure not only the continued formation, but the maintenance of an active, adsorbent, and hydroxide floc.
The mechanism is not unlike the reactions occurring in an activated alumina system, with the exception that the adsorptive media process requires no regeneration and can be backwashed like a conventional sand filter. The backwash water can be decanted and reclaimed allowing approximately 99 percent recovery and water recycle. Since the backwash water is non-hazardous, it also can be drained into a sanitary sewer.
ED and EDR Processes
Electrodialysis (ED) is an electrochemical membrane process initially developed for the treatment of saline or brackish waters. Instead of hydrostatic pressure, the process uses an applied direct current (DC) voltage to move dissolved anions and cations from alternate cells through semi-permeable membranes. This purifies a portion of the feed water, while concentrating another. While capable of removing arsenic to low levels, the process is equipment-, energy- and labor-intensive. It also creates a concentrate that must be disposed of, and is quite wasteful of water.
Electrodialysis reversal (EDR) is an ED process, which reverses the polarity of the electrodes on a controlled time cycle, which reverses the direction of ion movement in a membrane stack. Reversing polarity provides automatic flushing of scale-forming minerals from the surface of the membrane. EDR typically requires little or no pretreatment to minimize fouling of the membrane. ED/EDR systems are not considered to be economically viable for any but very small installations.
Nano-filtration
This process, also known as "membrane softening" uses an ultra-low-pressure membrane designed to allow only passage of particles less than 1 nanometer in size. It is very efficient in the removal of dissolved matter, but is, of course, not selective for arsenic only. Like all other membrane processes, extensive pretreatment is necessary to prevent fouling of the delicate and expensive membranes caused by particulate matter, scaling or biofouling.
CAMP Systems
The coagulation-assisted membrane process (CAMP) is considered to be a promising technology for arsenic removal because it can be applied over a wide range of water quality that contains high turbidity, iron, manganese, sulfate and nitrate. Low-pressure membranes (e.g., microfiltration and ultrafiltration) are very effective in removing particulate arsenic, but without a pre-coagulation step, low-pressure membranes are ineffective at removing soluble arsenic.
Metal-based coagulants, such as ferric chloride, can be used to bind the arsenic, which is removed with the ferric floc on the membrane. The use of low-pressure membranes eliminates the breakthrough of arsenic-laden coagulant flocs (a typical occurrence with conventional granular media filters) by taking advantage of the membranes' particle barrier. Factors affecting the CAMP system include ferric chloride dosage, pH, mixing and floc formation (contact time). As with all membrane processes, provision for adequate pretreatment to control feed water quality should be taken to protect the membrane from fouling caused by particulate matter, scaling and biofouling to optimize membrane performance and life. Disposal of the reject coagulant (which is not considered to be a hazardous waste) can be to a sanitary sewer.
Report Abusive Comment