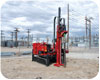
Direct
push rigs, like the 9500-VTR PowerProbe, work best in unconsolidated conditions
like sand and clay. Many also have augering capabilities. Photo by AMS
Direct Push Drilling Technology (direct push) allows for a wide variety of Direct Push Tooling (DP tooling) and instrumentation to be advanced into a subsurface lithology. This is conducted using a combination of the static weight of a direct push rig, hydraulic down pressure and rapid hydraulic hammering. For some direct push instrumentation, such as CPTu, rapid hydraulic hammering is not used.
Direct push can be used when subsurface soil/lithology is unconsolidated and displaceable, as is the case with sand silt, clay and small gravels. Compared to other types of drill rigs, the benefits of direct push for environmental drilling are: a small volume of or no unwanted waste material; tooling that is easy to handle and maintain; ease of proper decontamination; a small volume of decontamination waste material; no use of oils, greases, foams, or anti-seize compounds; ease of mobilization/demobilization, set up, operation and maintenance; and, because the rigs are generally smaller, they are ideal for limited access and remote areas.
The main activities are: soil sampling; groundwater sampling; soil gas sampling; installation of small diameter prepacked screen groundwater monitoring wells (direct push wells); installation of temporary groundwater monitoring wells; geotechnical testing and sampling to be used in remedial design; pilot studies; remedial injections, installation of conventional remedial wells; and angle borings/direct push wells.
AMS manufactures a wide variety of PowerProbe direct push drill rigs that can be installed on trucks, track carriers, tractors, skids, trailers and ATVs/UTVs, or can be standalone units.
Many direct push drill rigs have dual-combination types of drilling such as direct push and augering. Having an auger capability on a direct push rig can enhance the capability and effectiveness of direct push. A simple example of this is to auger through a relatively shallow and thin hardpan, and then telescopically direct push for the remainder of the depth of the boring.
By having multiple types of drilling, the rig can be more versatile, handling unanticipated subsurface lithologies and changing scopes of work for capabilities such as environmental drilling techniques, as well as geotechnical investigations. A direct push rig can be equipped with an auto-drop hammer or conventional SPT hammer to conduct Standard Penetration Tests, also sometimes referred to as “blowcount testing.” Also, by having a dual-combination type and capability drill rig, there are many capabilities with just one drill rig.
For environmental drilling activities, it is important to know and understand the site facilities, underground utilities, have a work plan or job specification, and use applicable standard operating procedures (SOPs), whether they be from ASTM International, customer-specific requirements, regulatory requirements (federal, state and local), or other. It is possible that the entire project combines standard operation procedures from all of the mentioned contributors.
As with all drilling and subsurface contamination there is a risk of danger to human health and safety. This makes detailed plans for the work and worker health and safety critical. All potential dangers, conditions and considerations must be identified.
A work/sampling plan contains any know prior information that will help the investigators conduct the investigation. Some valuable information could be any known history of the site, such as any information concerning the source, age of release, and previous subsurface contaminants on or adjacent to the subject site. Proposed soil boring and groundwater monitoring well locations are presented, and how samples are to be collected and prepared for submittal to an appropriate analytical laboratory for analysis. Also in the work plan are details about overhead and underground utilities, along with how to cut concrete or asphalt, the sample collection plan (depth, interval, quantity to initially be submitted, volume for analysis required, quality control), field monitoring and laboratory analysis.
Laboratories can be either conventional or mobile.
Soil Sampling
Soil sampling with direct push can either be: single tube; dual tube; piston sampler; telescopic drill and sample; or other, depending on the scope of work and subsurface conditions.
Groundwater Sampling
Prior to installation of direct push wells, groundwater samples can be collected through a variety of direct push tooling. There are several types of retractable groundwater samplers designed to sample groundwater where contaminants are dissolved in the upper/highest level of the groundwater table. There are also groundwater samplers for determining the conditions of the groundwater when a contaminant is possibly sinking within the groundwater.
If it is not possible or practical to sample through DP tooling, temporary groundwater monitoring wells can be installed.
If a long-term groundwater monitoring program is needed at the site, direct push wells can be installed.
In addition, where it is not possible or practical to install long-term groundwater monitoring wells, temporary wells can be installed.
Direct Push Groundwater Monitoring Wells
Direct push wells are approved and accepted by federal and state regulatory agencies and ASTM International has several methods and/or procedures directly related to the use and installation of direct push wells. The sizes of direct push wells range from -inch nominal inside diameter to 2-inch inside diameter. The practical achievable depth is based on lithology and the desired well ID size, but in general, less than 80 feet below ground surface (bgs) is the average depth; although it is possible to install direct push wells over 100 feet BGS.
They can be secured exactly like conventional wells and development of the prepacked section can be a simple surging. They can be used to calculate gradient magnitude and direction, and there is a variety of small-diameter instrumentation that can accurately take depth measurements, measure useful parameters and collect samples.
Once a subject site has been properly characterized, a precise and strategic remedial investigation can be conducted. Depending on the contaminant type, subsurface lithology and applicable regulatory requirements, a remedial action plan can be drafted based on the initial site investigation alone. If a pilot study needs to be conducted to determine the radius of influence for a particular remedial action, it can also be conducted with a direct push drill rig.
Once a remedial action has been completed, verification borings can be quickly and accurately conducted with a direct push rig to confirm the success of clean up or if additional remedial activities need to be conducted to clean the site up (restore the site) prior to requesting case closure.
In general, the limitations are the inefficiency in direct push activities at depths greater than 100 feet BGS and lithology. Direct push should not be used in bedrock and other consolidated subsurface lithologic formations.
This only describes the general advantages and basic capabilities of direct push for environmental drilling. It does not describe many important details and regulatory requirements that need to be taken into account prior to beginning any field activities of environmental drilling. ND
The purpose of environmental drilling is
• To identify the type, level/concentration and extent of contaminated soil.• To determine details regarding the subsurface lithologic condition.
• To evaluate if groundwater has been impacted or has the potential to be impacted by contamination.
• To sample groundwater and/or install long-term groundwater monitoring wells.
• Successful cleanup/remediation of contaminated soil and groundwater.
• Site Closure – the documentation for and final approval of and successful cleanup of the contamination for which the investigation and cleanup was caused.
• Ultimately, the goal is to protect and/or restore groundwater resources.
Report Abusive Comment